Job Opportunities
Sorry, the page you requested could not be found
This might be because:
- You have typed the web address incorrectly, or
- the page you were looking for may have been moved, updated or deleted.
Not ready to apply?
Join the Jabil Career Network!
Learn about upcoming career opportunities and events at Jabil
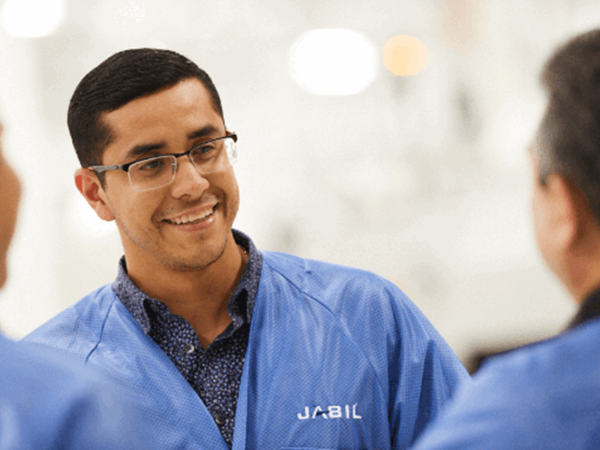.png)